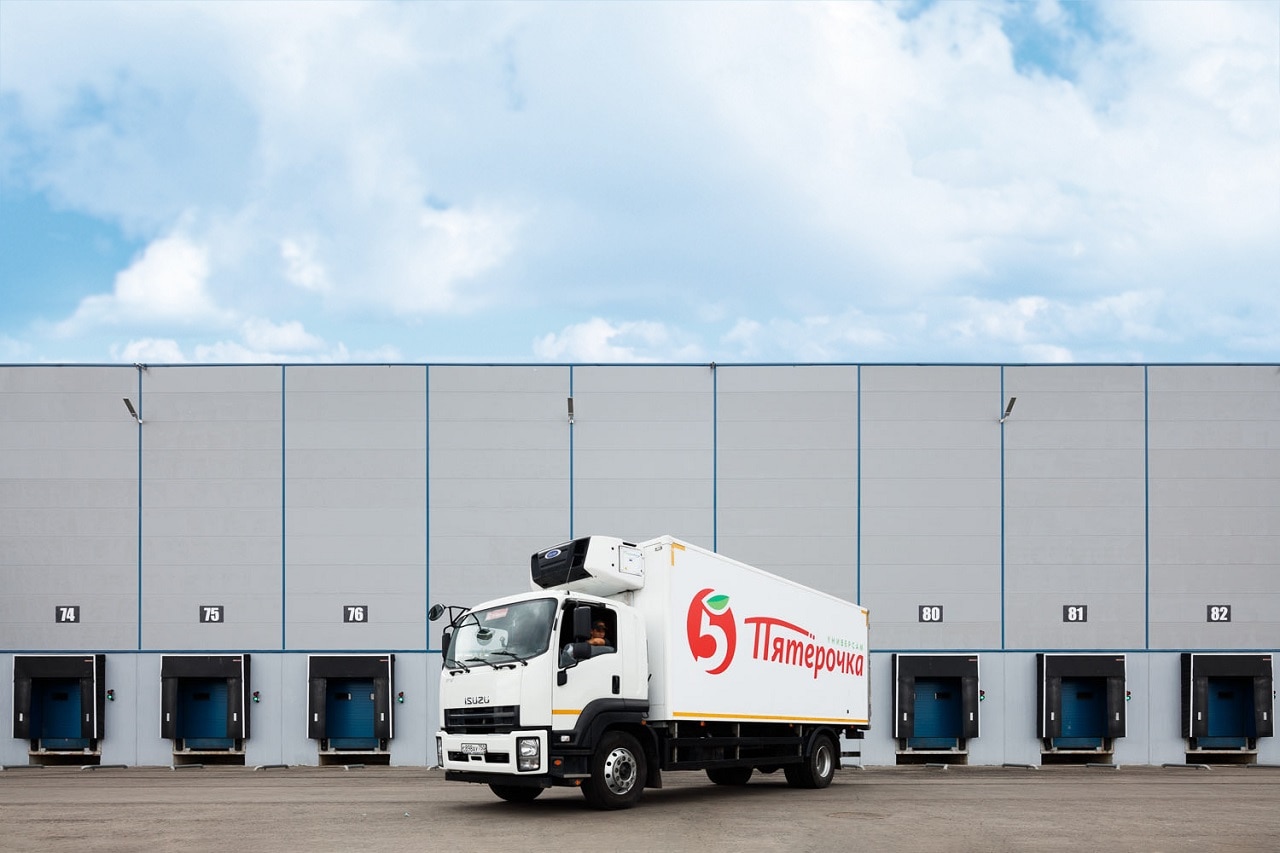
infrastructure
1.6.1 Logistics
Our logistics operations play a vital role in providing efficient, reliable support to each of our format’s CVPs. Pyaterochka runs its own logistics, while Perekrestok and Karusel share infrastructure, but we are also leveraging synergies between the logistics infrastructures of our formats in remote regions.
As of 31 December 2018, we operated 42 DCs with a total floor space of 1,179 thousand square metres, providing sufficient coverage for the Company’s rapidly expanding operations.
X5 Retail Group’s company-wide SLT level (order processing based on timely deliveries) remained stable at 90%, while centralisation increased from 93% in 2017 to 95% in 2018.
How we manage logistics
Logistics are managed from the X5 Corporate Centre, which sets standards for, and monitors the performance of, our DC operations. The head office also acts as a hub for the sharing of best practices and technologies between formats, as well as the centralised analysis and planning for logistics infrastructure expansion. X5 Retail Group DCs all utilise an automated warehouse management system (WMS) that includes features like voice picking and weighing technology.
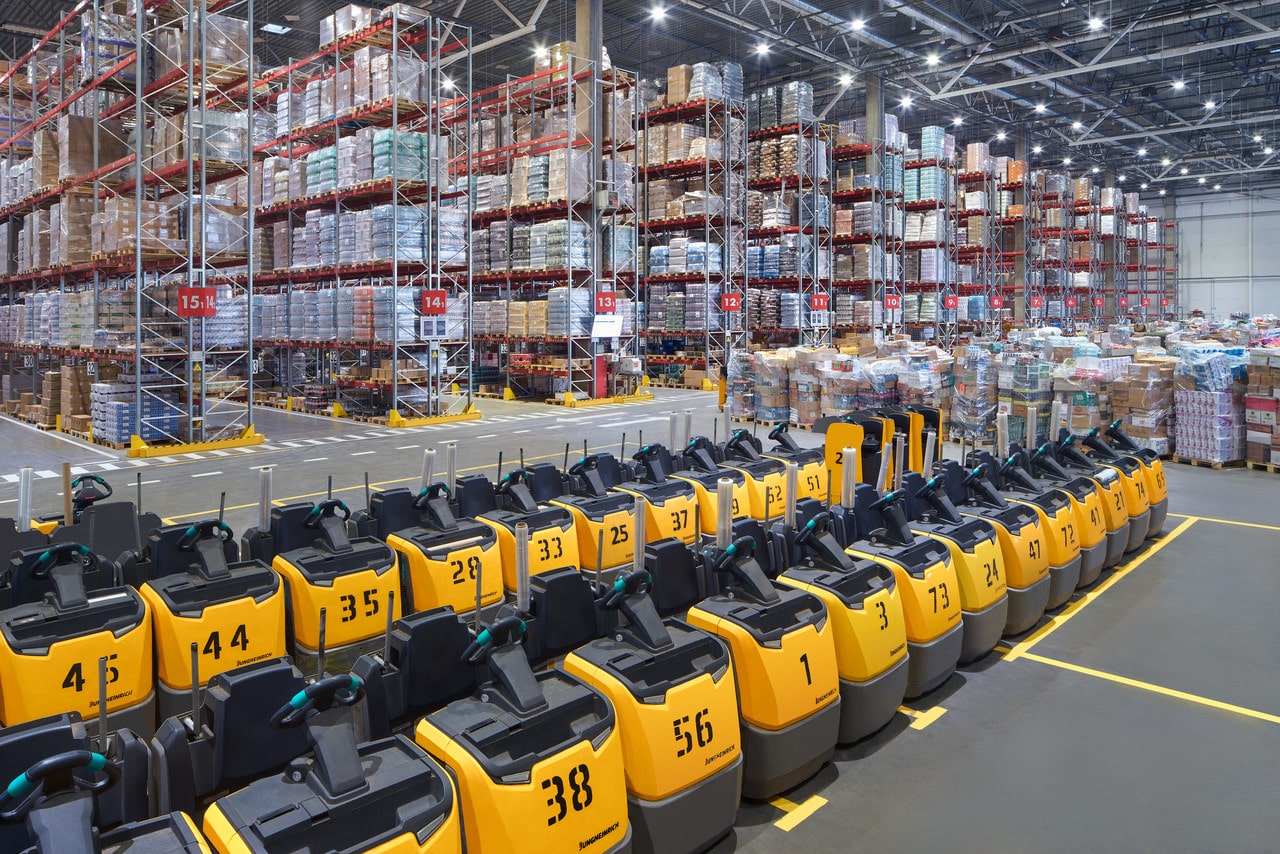
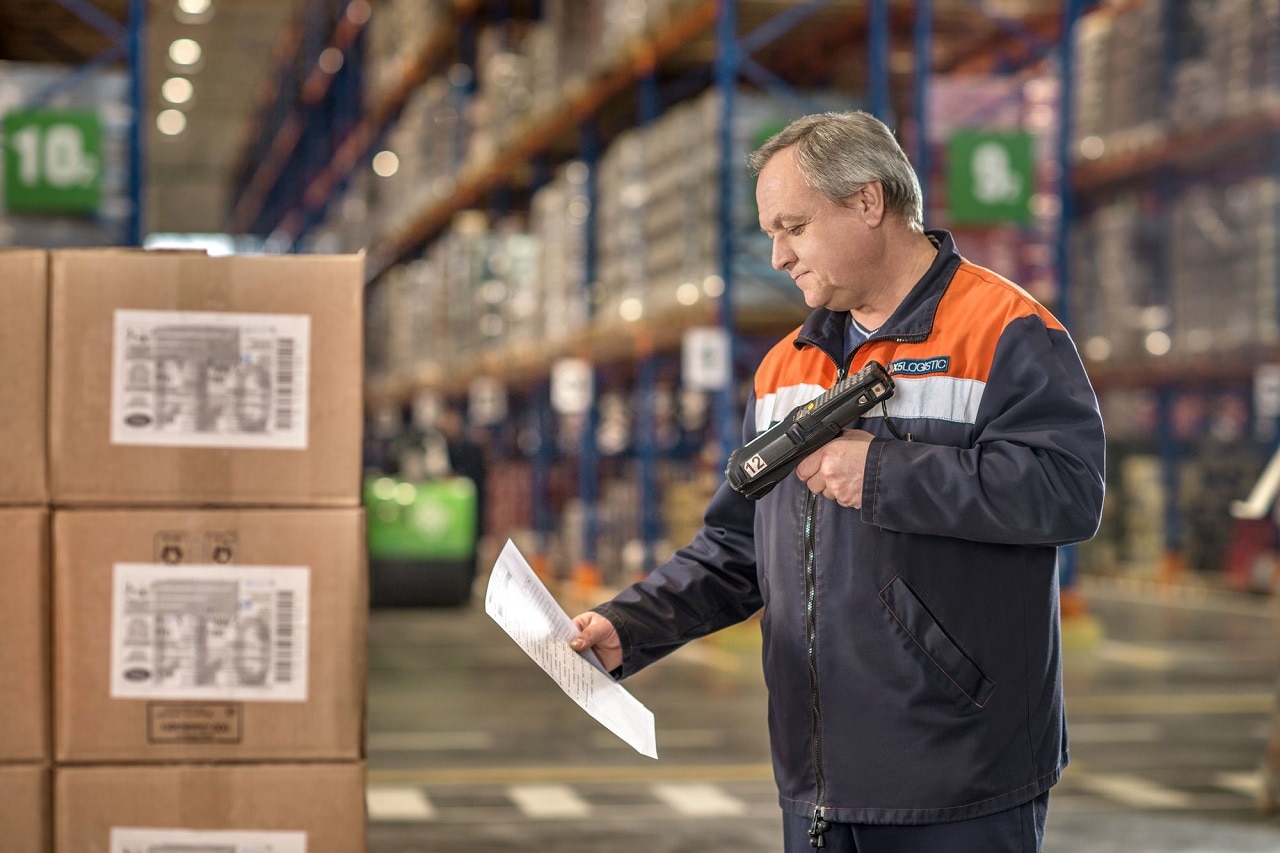
Logistics and Transportation Strategy
Throughout 2018, we worked to implement X5 Retail Group’s Logistics and Transportation Strategy to 2025, which was adopted in 2017 and covers plans for the development of our logistics operations.
The strategy focuses on reducing costs, cutting delivery times and ensuring the availability of a wide assortment of goods on our stores’ shelves. The strategy was developed to enable X5’s logistics to:
- Support the unique CVP of each retail format
- Respond to forecast demand through 2025 for each specific location
- Enable each format to achieve target market share, expanding operations based on the planned number of stores while reducing share of costs
- Allow formats to manage their own supply chain operations while in parallel seeking and implementing opportunities to achieve synergies
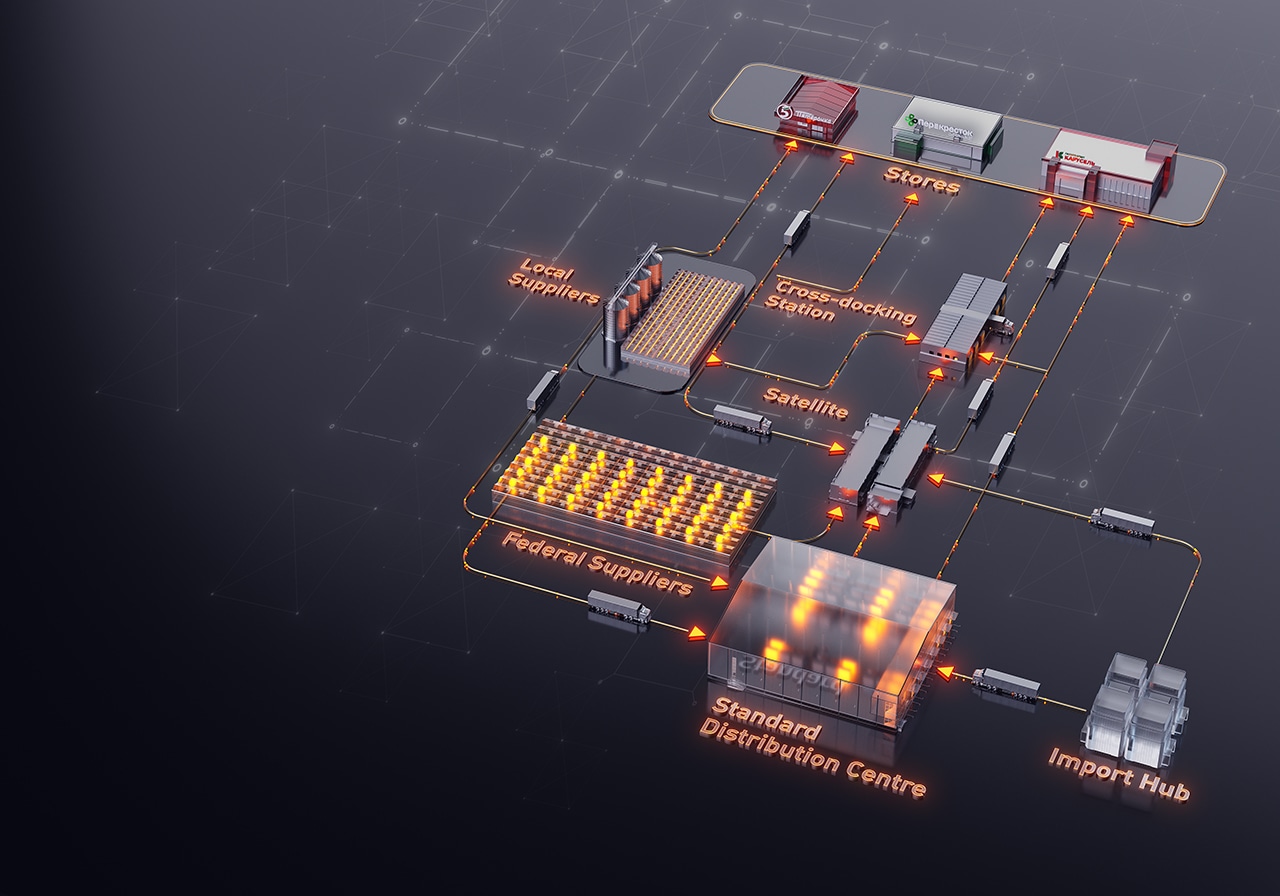
infrastructure
Pyaterochka operated a total of 30 DCs with an area of 892 thousand square metres as of 31 December 2018. The format opened three DCs with a total area of 70,036 square metres in 2018. Pyaterochka’s scale and geography of operations require a well-run, modern and efficient logistics infrastructure to enable the format to provide a reliable supply of high-quality goods to the shelves of 14,431 stores (as of 31 December 2018) in 64 Russian regions for every one of the 4.6 billion customer visits that we enjoyed in 2018.
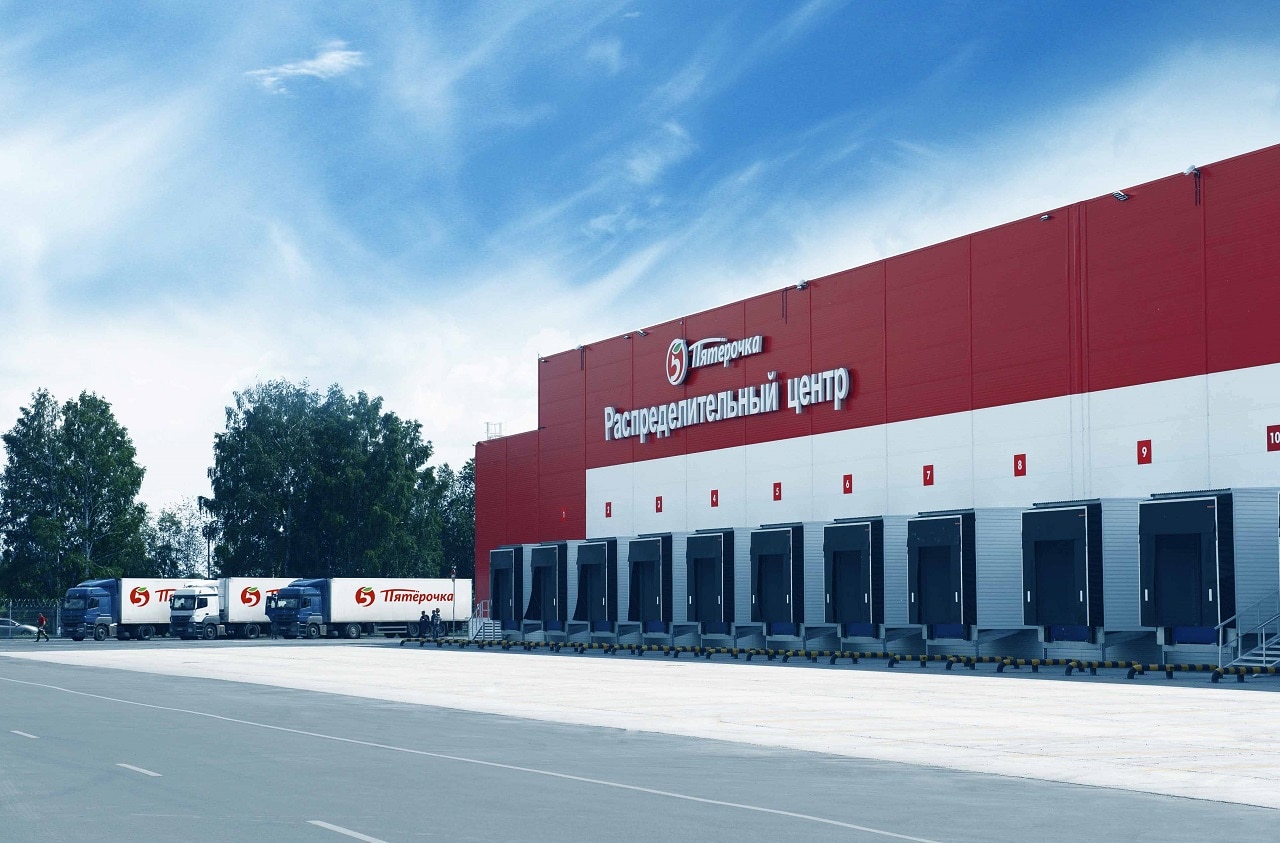
Key highlights for 2018
- Total throughput at existing DCs rose by 93% year-on-year
- Opened three new DCs, increasing total DC area for the Pyaterochka format by 70 thousand square metres year-on-year
- Improved operational efficiency of DCs: per-unit costs declined by 11% year-on-year, while the overall working rate reached a record 87 boxes per hour
- Leveraged synergies with other X5 Retail Group formats: our DC network increased the volume of boxes handled for large-format stores by 91% year-on-year to 2.2 million
Optimising transportation costs
One key area of focus in 2018 was optimisation of transportation costs, with a focus on further development of the Transportation Management System and increasing the share of automated route planning, which was launched in 2018 and reached 50% by the end of the year. This has significantly improved planning and routing accuracy:
- The vehicle activity ratio increased from 65% at the beginning of 2018 to 73% by the end of the year
- Turnover in the areas within 150 km from DCs improved by an average of 18% in 2018 following the introduction of multisectional resource planning
- Warehouse planning processes have been enhanced:
- Planning now covers the entire 24-hour throughput of goods, as opposed to 3-6-hour intervals in 2017
- The time required for route planning decreased from 16 hours to 10 hours, which improved plan fulfilment monitoring
- Planning algorithms have been introduced to even out the hourly loads on DCs and to analyse performance
- Delivery planning within a 6-hour window reached 91% in 2018, up from 67% in 2017
- Reduction in labour time required for the planning process has enabled route-planning staff to focus on monitoring standards and optimisation of transportation costs
Personnel development
- We focused on personnel development in 2018 with the launch of the Logistics Academy, a joint project with METRO Cash & Carry and Coca-Cola HBC that trains promising managers from the Logistics Department in leadership and effective project management. Candidates are nominated from the selected talent pool by macro-region heads. Programme students are required to develop projects that are presented to an expert jury upon graduation from the Academy.
Improving processes
- We updated our logistics business processes in 2018 with a focus on reliability, stability and coordination. These affected product life-cycle processes, as well as places where these processes intersect with management processes.
- We also developed our electronic document interchange (EDI) systems in 2018, extending the integration with suppliers to include seven new protocols. Pyaterochka currently has the broadest integration of EDI among retailers in Russia.
Plans for 2019
- One of our key areas of focus for 2019 will be innovations. We are already testing a new WMS in our Saratov DC, and we plan to migrate our first DC to the new system in the second half of 2019.
- We are also testing the robotisation of the storage of fruits and vegetables, autopilot for forklifts and automated assembly of small items.
- We are also working with the Commercial Department to launch a new packaging line in Krasnodar, which will add to Pyaterochka’s existing facilities, which include 14 banana ripening stations (eight owned and six external), as well as a watermelon binning service.
Our larger-format stores share logistics infrastructure that is fine-tuned to their needs. As of the end of 2018, Perekrestok and Karusel jointly operated 12 DCs. We are constantly modernising and expanding our logistics infrastructure to support the growth of our business, enhance efficiency and ensure that we can provide customers with a reliable supply of high-quality goods at every store that we operate.
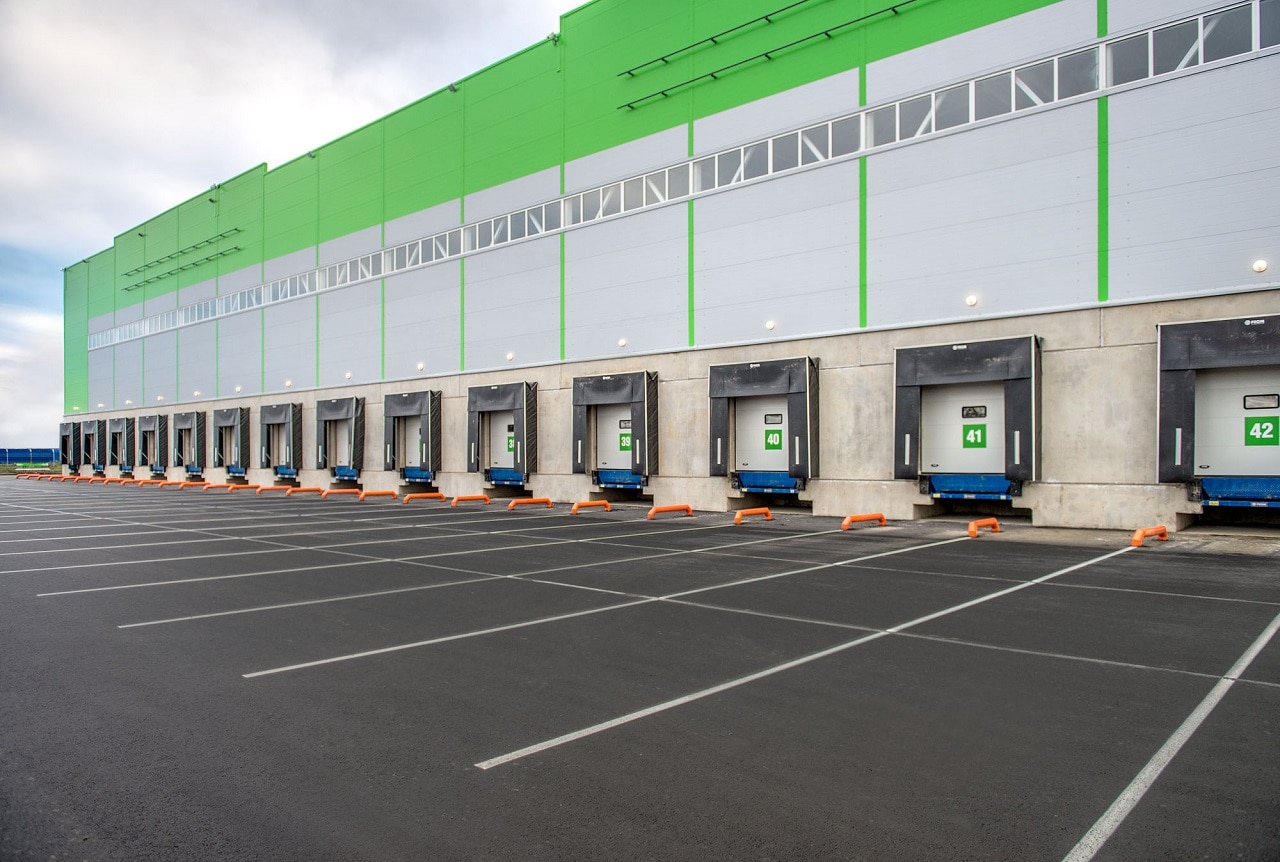
Key highlights for 2018
- Further developed and optimised the efficiency of our regional logistics, with the share of supplies delivered directly to regional DCs increasing by 8% in 2018
- Expanded synergies with Pyaterochka for supplies to remote regions
- Increased DC productivity with the use of new technologies
- Improved availability of goods
- Increased the share of direct imports, especially in fruits and vegetables from 23% in 2017 to 28% in 2018
- Launched a banana ripening complex at the Sofino DC in Q1 2018
DC network and supply chain management
- Launched the new Businovo DC in Moscow for the storage and processing of frozen products
- Temperature-controlled facilities for fruits and vegetables were built or refurbished at regional DCs
- Expanded shared use of DC infrastructure with Pyaterochka in regional hubs
- Continued transferring suppliers to direct deliveries in regional hubs: the share of direct deliveries to regional DCs increased by 8% year-on-year
- Improved DC load management and kept intra-week volume fluctuations within the maximum threshold of 15%
- Introduced a new supply chain that enables optimisation of inter-branch transport
- Implemented a methodology for differentiated management of delivery schedules to adjust for seasonal volumes without disrupting the overall capacity of the DC
- Continued to increase the share of direct imports: direct imports of fruits and vegetables at Perekrestok accounted for 28% of volume in 2018
- Implemented the Collaborative Planning, Forecasting and Replenishment (CPFR) project together with suppliers
Inventory management
- Reduced DC inventory levels by 8% (0.6 days) on average year-on-year, and by 23% (1.7 days) in Q4 2018 year-on-year
- Further developed the Sales and Operations Planning process with the launch of demand planning for regions, which helped increase forecast accuracy by 2% year-on-year
- Completed rollout of JDA for the fresh category, with implementation planned for ultra-fresh and fruit and vegetables in Q1 2019
- Increased availability of goods that are in the top 30 in terms of turnover by 7% year-on-year
- Achieved target of 95% availability of promo goods in Q4 2018
- Launched big data analytics to improve the accuracy of sales forecasting
- Reduced store opening time by one day thanks to packaging based on merchandising groups of similar goods
Plans for 2019
- Implementation of JDA across the entire assortment
- Start implementation of the new WMS
- Upgrade store shelf replenishment management with the help of the WMS targeted storage system
- Transition to the new Transportation Management System to standardise all transport management across X5 Retail Group
- Strengthen focus on availability in the fresh and fruits and vegetables categories
- Automate replenishment for promo goods
- Continue development of CPFR project with suppliers
- Launch project to create a shared global master data register of goods together with suppliers
- Launch fruit and vegetables packing lines for direct imports at the Sofino DC