1.7.5 Occupational health and safety
Occupational Health and Safety Strategy
Protecting the health and well-being of our employees is a top priority for X5. Occupational Health and Safety (OHS) measures aim to reduce injuries and occupational diseases, as well as improve working conditions, which ultimately leads to greater efficiency.
The main objectives of our OHS strategy are:
- Protecting the health and safety of our employees
- Ensuring that our OHS performance is in line with corporate standards and applicable laws
- Ensuring the best possible protection for workers in emergency situations
- Reducing the number of accidents at our facilities
Policy highlights
The main internal document governing occupational health and safety at X5 is the Occupational Health and Safety Policy.
The main aspects covered by our OHS Policy are:
- Ensuring OHS for our employees by taking preventive measures to avoid injuries and health impairments
- Ensuring that we have a functioning OHS management system and continuously improving it in accordance with changing legislative and other regulatory requirements in the area of occupational health and safety
- Ensuring that employees are informed about working conditions and OHS in the workplace, about health risks and any compensation and benefits they are entitled to
- Improving employee training in the area of occupational health and safety
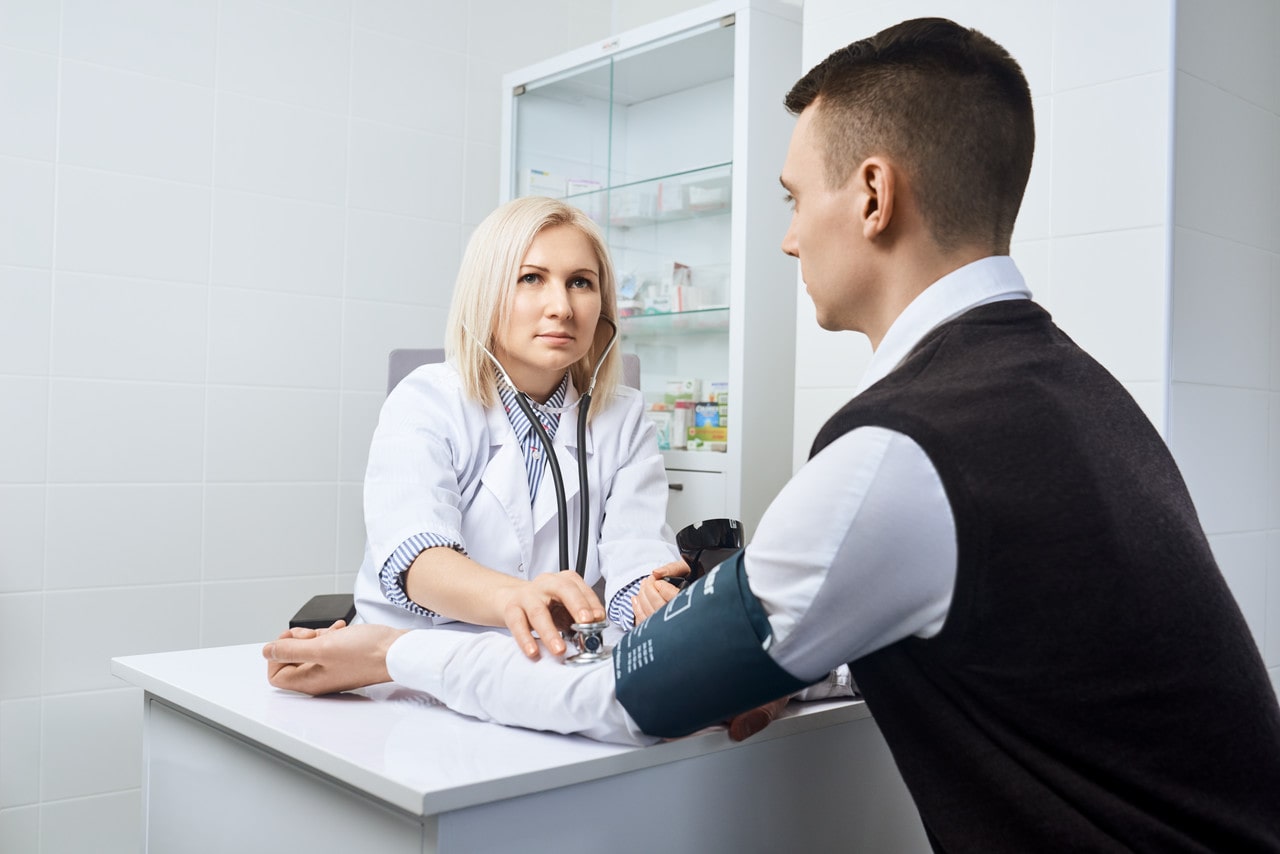
Implementation of our Occupational Health and Safety Policy is the purview of the Corporate Centre’s Occupational Health and Safety Department, together with key managers in each of our retail formats. Each retail format has its own occupational health service that employs from five to 40 people.
These services are mainly responsible for the following:
- Ensuring that workplaces are safe and secure
- Sharing information about workplace health and safety
- Supporting X5’s Occupational Health and Safety Policy by studying and analysing occupational risks
All of the Company’s work in the area of OHS complies with Russian Federation regulations. We have developed a system of corporate standards and regulations on OHS that form a unified set of organisational, technical, sanitary and preventive measures aimed at ensuring safety and protecting the health of employees and their working capacity.
Company-wide KPIs to improve labour efficiency and to motivate employees to achieve better results also include elements related to OHS.
For example, one of the goals of the KPIs for our key OHS specialists is to conduct a special assessment of working conditions. This enables the Company to identify dangerous or potentially harmful workplaces and makes it possible to take corrective measures in a timely manner in order to rectify OHS violations, which in turn minimises the administrative penalties assessed by state regulatory agencies. Our policies also entail considerable monetary penalties for OHS violations.
System highlights
Improving OHS competencies
- We have made considerable efforts to establish a culture of responsible behaviour in the areas of OHS, fire safety and road safety
- In accordance with applicable legislation, all X5 personnel must undergo every type of compulsory OHS training in a timely manner through specialised organisations, distance learning courses and/or OHS briefings
- An important aspect of our activities is the engagement and motivation of employees to comply with safety requirements, as well as training and informing employees about safe working methods. Training is aimed at improving the competencies of employees in accordance with internal standards and best practices in the development of an OHS management system
- Training for blue-collar personnel takes place through special corporate courses that complement legally required training on OHS issues; a significant number of programmes and instructions on OHS issues have been issued, which are designed for high-volume staff training and for a variety of target audiences
- X5’s main OHS documents are accessible to employees on each retail format’s intranet site
- We ensure that best industry and global practices are studied and applied as part of our process of continuous improvement
Prevention of workplace injuries
- We pay special attention to conducting assessments of working conditions
- To assess the impact of hazardous and potentially harmful conditions in every workplace within X5, health and safety engineers across all divisions in the Company carried out a special assessment of working conditions. The results of the assessment indicate that all workplaces meet the requirements of OHS legislation, with the exception of 200 potentially hazardous ones where loading and unloading work is carried out in warehouse refrigerators at distribution centres. Employees are entitled to compensation and benefits in accordance with applicable legislation for working in hazardous conditions. We are working towards further improvement of working conditions and additional vacation time for these employees.
- All X5 employees are provided with modern protective gear designed for the specific working conditions at each workplace.
Protecting the health of employees and customers
- In order to protect public health and the health of employees, as well as to prevent the occurrence and spread of infectious and occupational diseases at X5, mandatory pre-employment and periodic medical examinations are carried out for all employees of commercial facilities and the Transport Department. Should signs of an infection be discovered, the employees concerned are not allowed to come to work and are sent for further treatment.
- For preventive purposes, flu and other legally required vaccinations are provided.
Managing occupational risks
- The occupational risk management system developed in 2018 makes it possible to minimise the likelihood of accidents and emergencies. The system establishes risk ratings, determines the responsible parties for various risks, and allows for the development of risk management action plans and oversight of their implementation.
- Risk assessment involves an annual review and, if necessary, the addition or removal of a risk in order to achieve the required degree of control over those factors that entail an occupational health risk, the establishment of an advanced occupational risk management system that covers every workplace within X5, and keeping the system up to date
- Work is under way to develop a risk register for all workplaces, which will enable all managers and personnel to focus on eliminating or reducing the impact of potential hazards on employees, as well as to draw up, in a timely manner, corrective plans aimed at improving working conditions
- In order to achieve this goal, X5’s OHS Department intends to develop innovative approaches to the implementation of regulations and methods aimed at protecting workers’ health and labour rights
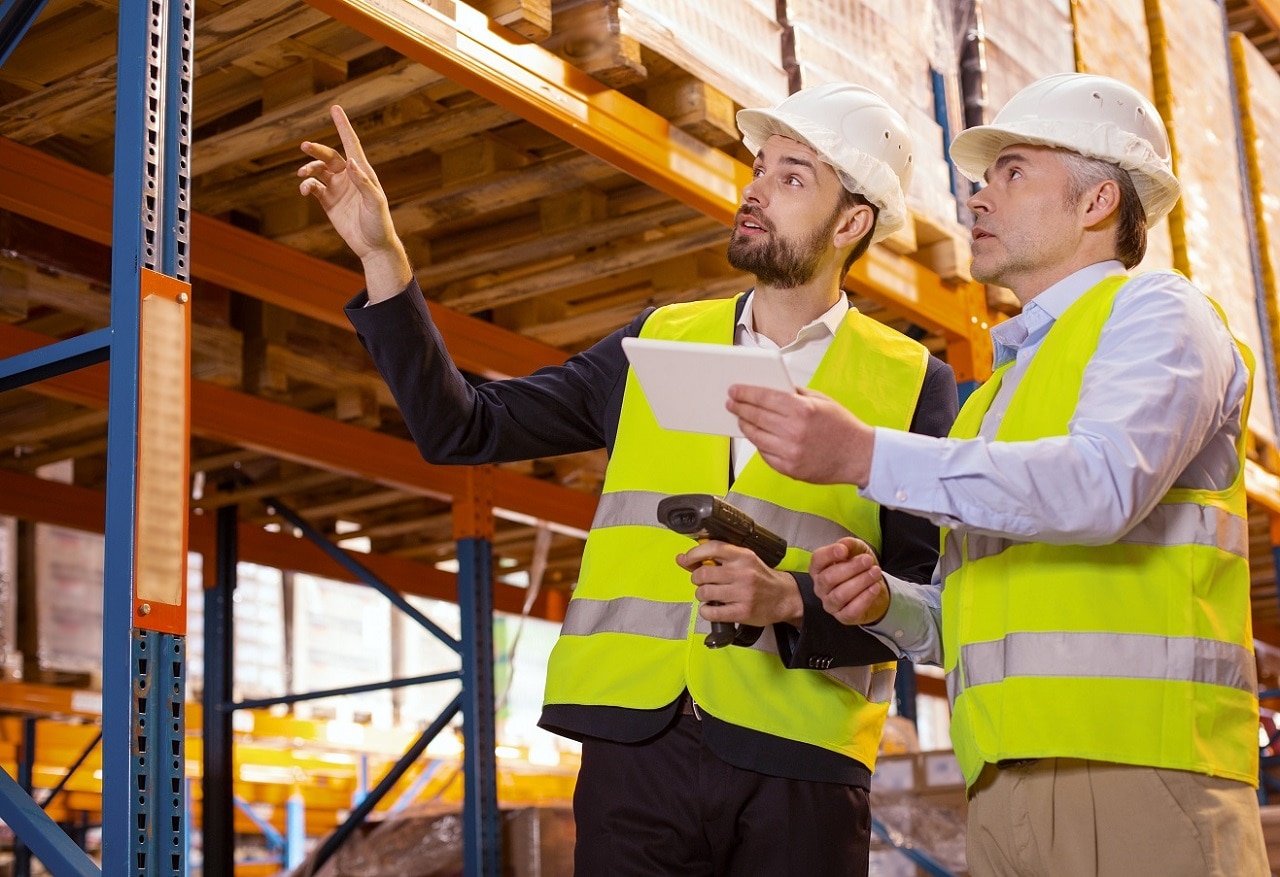
Investigating incidents and accidents at our facilities
- We have developed and introduced an incident/accident investigation procedure, whereby every case is investigated and a plan is developed for further action aimed at eliminating the causes of the incident and preventing a recurrence of the incident in future
- We provide accident insurance for our employees. All employees are covered by insurance as part of their employment agreement
- The insurance indemnity is paid out to employee s in case of serious accidents or to their family members in the event of a fatal accident
- The accident rate is analysed on a quarterly basis, which acts as a mechanism for recording and providing notification in case of accidents and occupational diseases, as well as a mechanism for the regular collection of the statistical data needed to determine priorities when implementing preventive and protective measures. In 2018, X5 registered 19,291 incidents/accident cases. In 68% of cases, the issue was resolved within five working days.
Monitoring compliance with OHS legislation
- X5 has in place a system for monitoring working conditions and occupational health and safety at every facility that is based on the principles of self-monitoring, mutual monitoring and managerial oversight, while the system status is constantly monitored, and preventive measures are constantly being taken to reduce injuries
- To prevent accidents and emergencies at X5 facilities, internal audits are carried out, the main task of which is to identify violations of state regulations and standards, as well as Company regulations
- To reduce labour costs when conducting audits, we use checklists that were introduced by Russia’s Labour Ministry in July 2018 and integrated into X5’s OHS management system
- Based on the results of these audits, measures are developed to improve the safety of workplaces and to prevent risks to the life and health of employees; the monitoring of compliance with the safety requirements established by federal laws and other regulations is improved, as is the monitoring of discipline in the workplace
- At X5, monitoring of compliance with OHS legislation and financial oversight related to the implementation of OHS measures are carried out by the Department of Occupational Health and Safety and the authorised OHS personnel in each retail format. The Department systematically reports on the following to the Company’s management:
- the results of internal audits and assessments of compliance with the requirements of OHS legislation
- the results of external audits conducted by oversight bodies, including complaints and claims
- the results of incident investigations, as well as corrective and preventive actions
- measures taken by the retail format in question based on the results of previous audits
- information on changes in OHS legislation
- quarterly and annual injury reports
2018 performance highlights
- The Company strictly adhered to OHS and sanitation standards, as a result of which no cases of occupational diseases were reported
- In 2018, we recorded a decrease in the severity and frequency of injuries compared to previous years, which is associated with ongoing activities that contribute to the prevention of injuries and accidents and that are aimed at compliance with the requirements of state regulations concerning the minimum conditions for safe work
- State regulatory bodies conducted 38 external inspections of compliance with OHS legislation and found 32 OHS violations, which was fewer than in 2017, and issued orders to rectify violations of labour legislation within the established period
- Special corporate training courses were developed for distance learning on occupational health and safety for all blue-collar positions. In 2018, 62,828 blue-collar workers were trained, in addition to managers and specialists
- A safety Gemba walk was carried out in the Logistics Department, and an internal OHS audit was carried out at commercial facilities using checklists approved by Russia’s Labour Ministry, which will make it possible to avoid routine on-site inspections by state regulatory bodies and to reveal and eliminate OHS violations in a more comprehensive manner
Retail format | Number of inspections (external and internal) | Number of identified violations | Number of violations resolved within 5 days | Number of violations resolved in more than 5 days |
---|---|---|---|---|
Perekrestok | 741 | 6,346 | 3,663 | 2,683 |
Karusel | 77 | 35 | 25 | 10 |
Pyaterochka | 6,227 | 11,334 | 8,584 | |
Transport | 343 | 1,576 | 928 | 648 |
Total | 7,388 | 19,291 | 13,200 | 6,091 |
- The Automated Medical Examination project ensured that nearly 100% of employees underwent examinations, thereby minimising administrative penalties assessed by regulatory authorities
- Projects were introduced in the Logistics Department that ensured safe working conditions and increased labour productivity: this involved the mechanisation and automation of warehousing, reducing manual operations to the maximum extent possible (especially strenuous manual labour during loading and unloading operations), the installation of additional protective devices and BlueSpot warning alarms on electric vehicles, and many other projects that improved working conditions and the safety of employees in warehousing operations
- Thanks to X5’s participation in a state programme that provides financial support for preventive measures to reduce workplace injuries, a special assessment of working conditions was carried out at X5 that was financed by the Social Insurance Fund of the Russian Federation, which saved the Company about RUB 16 million
The increase in the number of inspections was due to the introduction of electronic checklists within the Company as part of the optimisation of business processes. The significant increase in the number of OHS violations was due to the expansion of the checklist as recommended by the Ministry of Labour. The main violations found were of an organisational nature:
- 80% involved improper documentation for staff briefings, lack of signatures in OHS journals
- 20% of violations were technical: the lack of fencing around equipment, the lack of warning signs, etc.
All violations are rectified as quickly as possible by technical services and department heads.
Total number of employee work days lost per accident
Number of accidents per 1,000 employees
Format | Number of accidents | Total | Work days lost | |||||||||
---|---|---|---|---|---|---|---|---|---|---|---|---|
Fatal | Severe | Minor | ||||||||||
2018 | 2017 | 2018 | 2017 | 2018 | 2017 | 2018 | 2017 | 2018 | 2017 | |||
Karusel | 0 | 0 | 1 | 3 | 12 | 35 | 13 | 38 | 859 | 1,158 | ||
Perekrestok | 0 | 0 | 1 | 2 | 24 | 11 | 25 | 13 | 936 | 600 | ||
Pyaterochka | 0 | 0 | 13 | 9 | 127 | 107 | 140 | 116 | 5,798 | 6,251 | ||
Transport | 1 | 0 | 2 | 4 | 18 | 17 | 21 | 21 | 1,428 | 1,247 | ||
Total | 1 | 0 | 17 | 18 | 181 | 170 | 199 | 188 | 9,021 | 9,256 |