1.7.2 Product safety and production quality
Our goal is to offer our customers nothing but fresh, high-quality products at every store we operate. In order to achieve this, we implement and adhere to rules and regulations that cover the entire supply chain, from before products are delivered to a warehouse or a store, and all the way through until they are in the hands of the consumer. The policies and systems that we implement and operate are in full compliance with Russian legislation and regulatory requirements and also aligned with global best practices in the food retail sector.
2018 in numbers
Pyaterochka
Perekrestok
Karusel
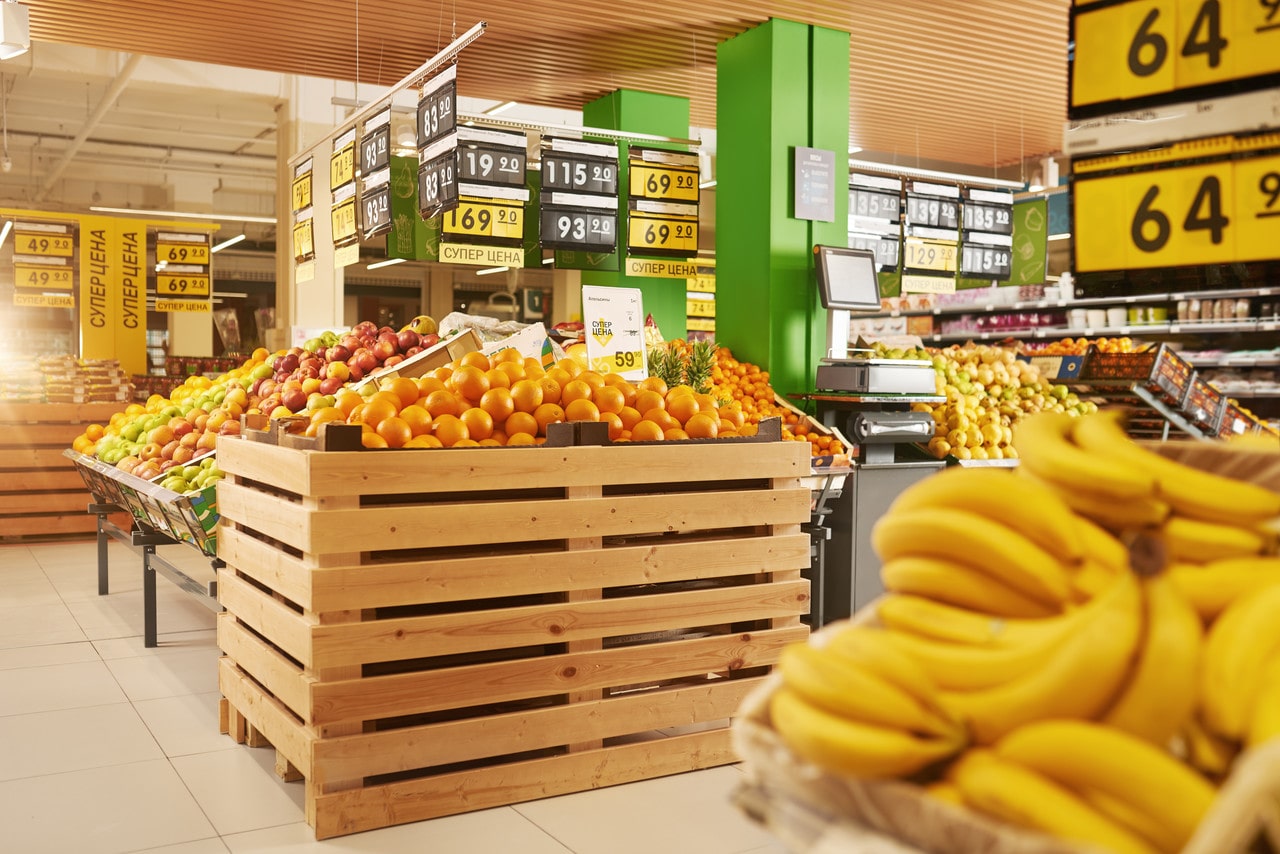
Policy highlights
Across all of our formats, we implement a clear set of rules and guidelines regarding the quality and safety of the products we sell. Our quality control systems cover our entire operations, from supplier audits to monitoring and checking the goods on store shelves.
We strive to constantly improve safety and quality control practices throughout our supply chain and retail operations. In order to do this, we seek, on a regular basis, recommendations from leading inspection, verification, testing and certification companies and then implement them in our day-to-day work.
As the largest food retailer in Russia, X5 works closely with federal regulators and decision-makers to draft documents, including food standards.
Each of our retail formats maintains its own quality and safety monitoring policies, but they are all based on the following principles:
- Ensuring food safety and social responsibility
- Understanding the current and future needs of consumers, meeting their stated and unstated goals, and aspiring to exceed their expectations
- Specifying the target quality level based on the demands of the consumer
- Establishing and developing mutually beneficial partnerships with producers and suppliers
- Creating and maintaining a corporate culture in which all employees are fully engaged and interested in using their knowledge and experience to achieve established goals
- Running all of our formats by using a process- and systems-based approach to the various stages of a product’s life cycle: starting with the development and entry of goods into our product range through production and sale to the consumer
- Introducing modern quality control methods to improve efficiency and effectiveness in terms of ensuring food safety
- Continuous improvement as an ongoing requirement
In order to maintain a dialogue with all business partners, X5 also works with industry associations, including the Consumer Market Participants Union, the Russian Union of Industrialists and Entrepreneurs, the All-Russian Association of SMEs (Opora), the Civic Chamber of the Russian Federation, the National Dairy Producers Union, the RusBrand Association of Branded Goods Manufacturers, the Seafood Processors Union and the RusProdSoyuz Association of Food Manufacturers and Suppliers.
System highlights
Each of our formats has its own Quality Department that is responsible for establishing safety and quality standards and product specifications at the format level, and all of these requirements are agreed with the respective Commercial Departments. The Quality Department receives and analyses the results of internal inspections and supplier audits and monitors whether standards are met. It is the shared responsibility of the Quality and Commercial Departments to respond to incidents of non-compliance by taking measures to eliminate shortcomings and help suppliers develop their systems or products properly. The two departments prepare periodic reports for management review. In addition, our retail formats regularly engage accredited international auditors to conduct audits of their suppliers, and they update quality specifications and standards for food products, private-label goods and packaging on an ongoing basis. X5 deploys the principles of hazard analysis and critical control points to ensure that its products are safe for consumers and the environment, and that they meet retail standards and customer needs.
Other quality assurance practices that we use include:
- lab testing and analysis of products at independent research and development centres and accredited research laboratories;
- staff training;
- safe storage and transportation of products;
- modern monitoring methods, innovative technologies; and
- supplier audits.
How it works in practice
Introducing goods into our product range
When introducing products into our product range, provided samples undergo comprehensive testing for compliance with our internal requirements and the laws and regulations of the Russian Federation:
- Verification of a range of documents that certify the quality and safety of products, as well as the protection of consumer rights.
- A tasting commission conducts a blind organoleptic evaluation of products and raw materials and assigns a score to each item.
- Accredited laboratories check compliance with the established requirements (microbiology, physical and chemical indicators), determine whether or not products are genuine, and issue test reports. Tests are carried out both for new products and during the process of monitoring goods that have already been supplied.
- Production status and a producer’s ability to deliver the required amount of a given product while meeting quality and safety standards is assessed (audited) by certified, independent experts together with management. Based on the results of an audit, a checklist with a comprehensive assessment is completed. Audits are divided into primary audits (pre-contract) and inspections (during the supply process).
Based on the results, management takes a decision about whether or not to introduce a product into the product range.
Management pays particular attention to the quality of private-label goods: for these goods to be introduced into the product range, a separate checklist is completed, and a different procedure is followed that involves more in-depth and stricter testing of suppliers.

Acceptance at distribution centres
Our DCs carry out testing to ensure that all incoming food products comply with X5’s standards, including regarding their appearance, as well as with Customs Union and Russian national regulatory requirements. X5’s quality control for fruits, vegetables and exotic fruits meets national standards and those of the United Nations Economic Commission for Europe, as well as X5’s own quality catalogue and acceptance criteria, including calibre, size and ripeness.
In 2018, Pyaterochka continued implementing its “Remote Acceptance” project at DCs and hubs. This project enabled the format to reduce losses of fruits and vegetables by using video monitoring and random sampling, and also by reducing corruption risks. Also in 2018, an upgrade of the “Remote Acceptance by Quality” project was launched, with additional control points established at every DC, which made it possible to speed up the acceptance of fruits and vegetables.
In 2018, Pyaterochka implemented a project to improve the monitoring of the supply of chilled goods from the supplier to the store shelf. As part of the project, all of Pyaterochka’s DCs and hubs were equipped with sensors that measure temperature and humidity data in real time. Also, all incoming deliveries of fruits and vegetables are accompanied by similar temperature sensors, and when the goods are accepted, the quality manager has access to information on the transport conditions; in case of critical deviations, the information is recorded by the sensor, and delivery is not accepted. Another project was launched in 2018 to integrate all temperature and humidity monitoring systems into a single operational monitoring system that will make it possible to monitor storage and transportation conditions for fruits and vegetables and fresh produce supplies in one place and to take prompt corrective measures in case of violations.
In order to improve the monitoring and analysis of product acceptance at DCs, a tablet-based system for accepting goods was developed, together with Perekrestok’s Logistics Department, and is being implemented for the following purposes:
- Product traceability (responsible inspector)
- Automation of the acceptance process: information is automatically entered into the system
- Optimisation of the work process (elimination of technical operations related to paper acceptance)
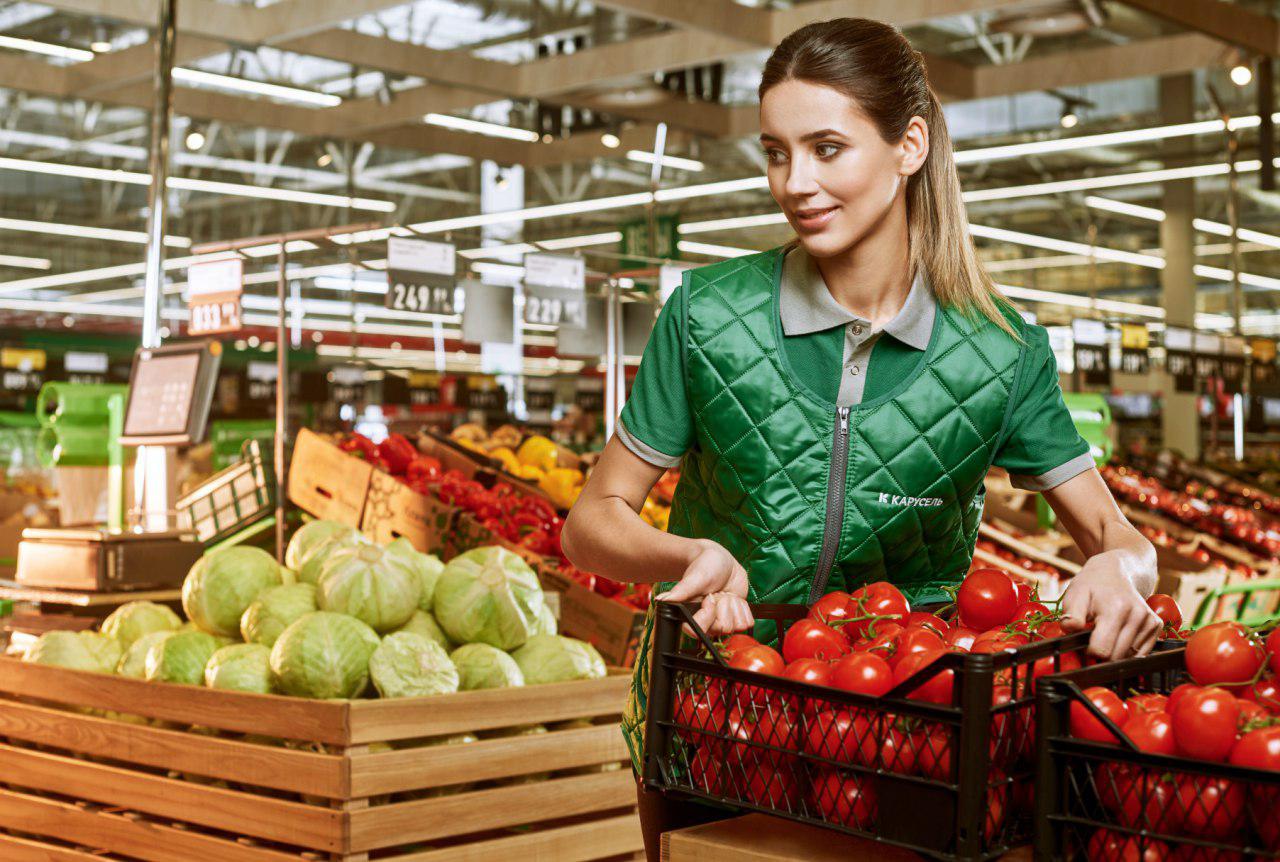
Quality control in stores
Under our Quality Hour programme, all products on our shelves are sorted and checked for quality and freshness every morning between 9 a.m. and 10 a.m. Pyaterochka store directors are personally responsible for product freshness in their additional role as “freshness directors”.
All of our formats regularly audit stores to monitor compliance with safety and quality standards, which means we are able to addres s issues quickly as they arise and improve the quality of the service we offer our customers.
2018 | 2017 | 2016 | 2015 | |
---|---|---|---|---|
Pyaterochka | 1,240 | 2,268 | 1,956 | 702 |
Perekrestok | 880 | 907 | 427 | 305 |
Karusel | 447 | 728 | 265 | 212 |
X5 total | 2,567 | 3,903 | 2,648 | 1,219 |
Audit of producers, including of private-label items
X5 Retail Group works with over 5,600 suppliers from Russia, the CIS, Europe, Asia, Africa and Latin America (over 1,400 new suppliers in 2018). As part of the selection and rating of suppliers, a supplier audit is required. The Supplier Audit Programme is available on the supplier portal along with a requirements checklist. All new suppliers undergo a mandatory audit to confirm that their production facilities are compliant with quality and food safety requirements.
In 2018, Pyaterochka launched a project to automate the supplier audit process, to refine its information systems for requesting an audit, to complete checklists and maintain audit schedules, and to automatically block suppliers that have not been audited. This will enable the Company to maintain audit statistics, to make sure that low-quality and unsafe goods do not end up on store shelves, and to simplify work with suppliers and to maintain a rating for them.
During the year, all of X5’s formats conducted audits of suppliers, when samples of product items were sent to independent, accredited testing facilities for analysis. This analysis was aimed at verifying products’ organoleptic, physical, chemical and microbiological properties and, in some cases, the declared ingredients, specifically to identify any that had been replaced with cheaper alternatives, as well as any use of food additives, artificial colourants, sweeteners or preserving agents not indicated on the label. Supplier audits by Pyaterochka resulted in 190 suppliers being barred from selling goods to the format, while Perekrestok’s audits led to 25 goods being barred from the assortment and one supplier being disallowed.
X5’s supplier evaluation criteria are applied across the group, so that all of our brands are able to use the audit results from one format. In addition, our call centres have established procedures for handling customer complaints about private-label products.
2018 | 2017 | 2016 | |
---|---|---|---|
Pyaterochka | 1,085 | 977 | 939 |
Perekrestok | 225 | 174 | 167 |
Karusel | 28 | 33 | 14 |
Interaction with consumers
In addition to a customer hotline (each format has a dedicated hotline), X5 regularly monitors social networks, blogs and online forums for potential complaints. We thoroughly investigate all customer comments and complaints about product safety and quality. This verification process may involve making control purchases and sending samples for analysis.
Interaction with public authorities and self-regulating organisations
In 2018, the Company conducted a pilot project called Svetofor (traffic light), which was initiated by the Federal Service for Supervision of Consumer Rights Protection (Rospotrebnadzor). Voluntary labelling under the Svetofor system involved color-coded information on food packaging depending on the levels of salt, sugar and fatty acids, based on recommended daily allowances of these substances. For these purposes, Rospotrebnadzor prepared guidelines on the colour indicators to be used for the labelling of food products in order to better inform consumers.
In 2018, paper veterinary documents were replaced by electronic versions that are completed in the Mercury Federal State Information System. This change not only made it possible to trace goods that are being monitored, but it also reduced the paper workflow and thus the costs associated with the process, resulting in tangible savings.